Mass Clean Energy Center Partnership Helps Engineering Researchers Advance Wind Power

Commercial wind turbine blades, which are made of fiberglass composite, can measure 200 feet or more in length and weigh many tons.
05/01/2021
By Ed Brennen
After two decades of steady growth, wind blew past hydroelectric as the leading source of renewable energy in the United States in 2019. Last year, wind turbines generated a total of 338 billion kilowatt-hours of electricity, or 8.4% of the country’s grid supply, according to the U.S. Energy Information Administration.
And there is more to come. In March, the Biden administration announced plans to add 30,000 megawatts (MW) of offshore wind energy — enough to power 10 million homes — by 2030, creating an estimated 80,000 jobs in the process. In Massachusetts, Gov. Charlie Baker recently signed climate change legislation that calls for the commonwealth to procure an additional 2,400 MW of offshore wind energy by 2027.
“It’s a good time to be in wind,” says Mechanical Engineering Chair and Prof. Christopher Niezrecki, who is director of WindSTAR, a collaboration between UMass Lowell and the University of Texas at Dallas. Funded by the National Science Foundation, WindSTAR is an Industry-University Cooperative Research Center (IUCRC) that aims to make wind energy more efficient, reliable and affordable.
Several faculty members from the Francis College of Engineering are helping advance the use of clean, renewable wind energy through research in areas such as wind turbine blade manufacturing and monitoring and workforce development. Their work is supported by the Massachusetts Clean Energy Center (MassCEC), a quasi-public agency founded in 2009 to develop a diverse and inclusive clean energy economy that can help the state achieve its goal of net-zero carbon emissions by 2050.
“Sustainability is a very important part of our mission in the Francis College of Engineering and across the entire campus,” says Engineering Dean James Sherwood, who has received more than $250,000 in MassCEC grants since 2017 for his research on composite blade manufacturing. “We have a lot of talent working in the wind industry area, and MassCEC has been a great partner for us in many ways, enabling us to leverage funding from federal agencies.”
While MassCEC works with UML researchers on clean transportation, high-performance buildings and net-zero grid technology, offshore wind energy has recently emerged as the leading focus area, according to Senior Program Director Ariel Horowitz.
“UMass Lowell has been really active, especially in leading some of these industry collaborations. Having that academic research and development presence around offshore wind positions the commonwealth really well to be a leader in the future,” she says.
MassCEC provides more than financial support for the university’s wind energy research. UML students have participated in its clean energy internship program, and faculty and students frequently conduct research at MassCEC’s Wind Technology Testing Center in Charlestown, Massachusetts — the largest testing facility in North America.
“It’s been a very fruitful and mutually beneficial collaboration. They’re an integral part of what we do,” says Niezrecki, who adds that it would have been much more challenging for WindSTAR to receive $582,000 in Phase II funding from the IUCRC program last year without MassCEC’s support.
Here’s a closer look at some of the research work funded by MassCEC:
Blade Manufacturing Automation
With thousands of wind turbines sprouting up this decade, manufacturers will need to ramp up the production process. According to Sherwood, wind blade production is a very manual labor process, and that labor accounts for about a third of the cost to make a blade.
“Because the wind blade industry works on such small margins, blade makers are reluctant to implement a new manufacturing technology without knowing the return on investment up front,” he says.
Sherwood just finished leading a research project in which Ph.D. student Stephen Johnson developed a software tool that uses a “technoeconomic model” to show wind blade makers if and how much time and money can be saved by adding a new automation technology to the blade manufacturing process.
“Before the blade maker spends millions of dollars on a new technology, they can use the model to study the impact of the implementation in a virtual environment,” says Sherwood, whose industry partners included General Electric, TPI Composites, Janicki Industries and Dassault Systèmes, as well as the National Renewable Energy Laboratory.
Sherwood received nearly $1 million in funding for the project, half of which came from the Institute for Advanced Composites Manufacturing Innovation, a Manufacturing USA Institute. MassCEC contributed matching funds through its AmplifyMass program, which funded the work of two mechanical engineering Ph.D. candidates: Johnson, who recently retired from a 35-year career at GE Renewable Energy; and Matteo Polcari ’14, ’16.
Johnson created a Microsoft Excel worksheet model that reads engineering drawings, looks at pricing information and computes (based on labor data collected from manufacturers) how much it will cost to make a blade.
“He came up with a way to reduce the cost of a blade by 3%, which represents significant savings when you’re talking about something that costs on the order of $250,000 each,” Sherwood says.
Working in parallel with Johnson’s Excel modeling, Polcari used DELMIA (a program from Dassault) to create a visual model of an entire wind blade factory.
“Matteo can literally insert a new technology into his full-factory simulation and see what repercussions you are going to have throughout the factory,” says Sherwood, who compared it to whack-a-mole. “You may make something better here, but then another problem may pop up elsewhere.”
Structural Monitoring
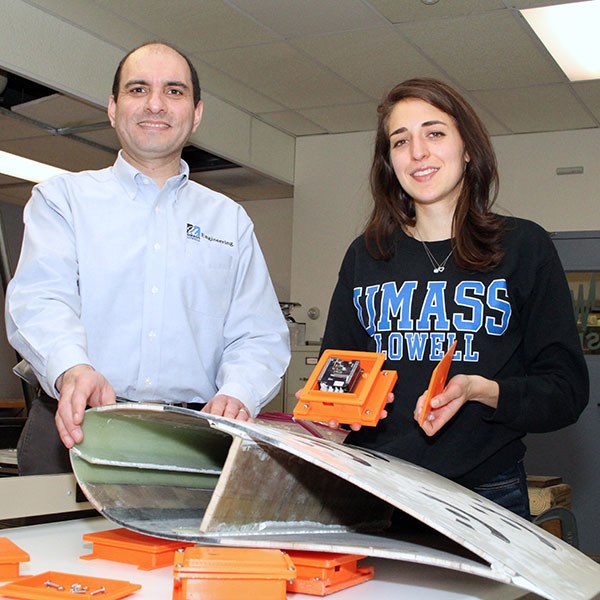
Mechanical Engineering Assoc. Prof. Murat Inalpolat, left, and Ph.D. student Jaclyn Solimine ’17 with a cross section of a wind turbine blade at the Structural Dynamics and Acoustic Systems Laboratory on North Campus.
“With help from the original MassCEC funding, we were able to branch out and get all these larger scale funds,” says Inalpolat, whose project uses low-cost, wireless microphones mounted inside the blade’s structural cavity to detect sound changes caused by blade defects or damage. Sound measurements are fed to a computer, which can automatically detect anomalies in the data.
With the average wind turbine requiring around $200,000 in maintenance over the course of its 20-year lifespan, Inalpolat says the acoustic monitoring system can lead to a “much less costly maintenance cycle.”
Inalpolat and two Ph.D. students assisting him on the project — Jaclyn Solimine ’17 and Caleb Traylor — are regular visitors to the Wind Technology Testing Center, where they piggyback on existing blade testing with their acoustic monitoring.
“I cannot tell you how convenient it is for us to be able to do research on turbines there. Without their help, it wouldn’t be possible to do some of our work,” Inalpolat says.
Workforce Development
To ensure that Massachusetts has enough qualified workers to fill the thousands of offshore wind energy jobs that will be created in the next decade, MassCEC awarded a two-year, $244,457 grant to UML last summer to analyze the local labor market and develop a defined track for undergraduate students who want to work in the field.
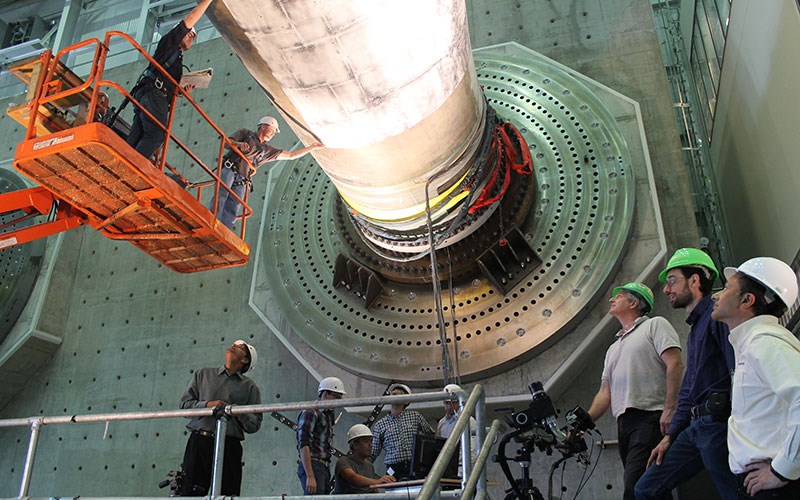
Wind Technology Testing Center Executive Director Rahul Yarala, lower left, checks out a project with Mechanical Engineering Chair and WindSTAR Director Christopher Niezrecki, right, and others at the MassCEC facility in Charlestown, Massachusetts.
Working with the nonprofit association RENEW Northeast, the team is surveying members of the offshore wind industry to determine their hiring needs. They are also partnering with the MassHire Greater Lowell Workforce Board to learn more about the demographics of the available workforce. One of MassCEC’s priorities, Hansen notes, is to ensure that previously underserved populations benefit from clean energy projects.
“MassCEC is committed to broadening participation of diverse groups that are underrepresented in the energy and engineering fields — which, of course, Lowell is well positioned to do because it is a Gateway City,” Hansen says.
Meanwhile, the team will assess the existing skills being taught in the engineering, sciences and business schools at UML to determine what would be applicable to the industry’s needs. The goal is to create a targeted, credentialed pathway that prepares students for a career in the wind energy field.
“It could be someone graduates with a mechanical engineering degree, but they took their technical electives and one additional business elective, and those things together fulfill this pathway,” says Hansen, who adds that students could also benefit outside the classroom. “You can bring in industry to do an offshore wind-specific capstone project for seniors, or you could have students do a co-op with a renewable energy company.”
Hansen says it is “amazing” how quickly the offshore wind industry has changed over the past five years — and how much it will grow in the next 30 years.
“Electricity usage in Massachusetts is projected to double by 2050, and that energy is expected to be about two-thirds offshore wind. So, we’re going to install more than the existing energy infrastructure, just in offshore wind, in the next 30 years,” he says.
And thanks to MassCEC, Hansen says UMass Lowell students will be prepared to step right into the emerging industry.
“This really is the future. It’s a huge opportunity,” he says. “If they join the offshore wind energy field, they have a job basically guaranteed for life.”