Students Turn Mold Designs into Reality
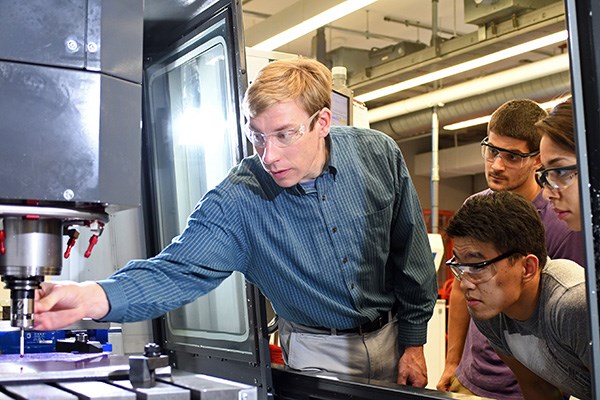
04/05/2017
By Edwin Aguirre
Many student-designed academic projects never leave the drawing board. Students can spend weeks designing and evaluating their concepts, but they never have the opportunity to create the actual products to test their feasibility and functionality.
However, students enrolled in the Plastics Engineering Department’s mold design engineering course, called PLAS.3730, have the advantage of carrying their ideas from concept to creation.
“During the semester, student teams will design a new plastic part, analyze its moldability, develop and produce the required tooling and finally use injection-molding machines to fabricate fully functional prototype parts,” says Assoc. Prof. Stephen Johnston, who has been teaching the course since 2008. “The coursework includes an introduction to the fundamentals of plastics mold engineering, which imparts to students an overall appreciation of how the process affects part quality and what the job of a mold engineer is like.”
Johnston says mold design courses like this are very unique. “There are a handful of other plastics engineering programs throughout the country that offer similar content and experiences, but to my knowledge none give the students the same level of design flexibility,” he notes.
Filling the Needs of a Growing Market
The injection-molding process involves forcing molten plastic material into a mold, where it solidifies and takes the shape of the mold. Injection-molded plastic parts are integral components of thousands of products across a range of industries, including automotive, medical devices, aerospace, consumer appliances, toys, electrical and electronics, plumbing, packaging and construction.
According to a recent industry report by Grand View Research, the global injection-molded plastics market was valued at nearly $200 billion in 2014, and it is anticipated to “witness significant growth in the near future on account of increasing plastics component demand across various end-use industries.”

From Simple to Elaborate Designs
Students are encouraged to be creative when designing their projects. Each team must design a new plastic part or improve an existing part design. Examples of early products include model toy cars, tops and planes, combs, drinking cups, utensils and measuring cups. Recent designs have become more elaborate, such as an earbud case, a ball maze and puzzle cubes, as well as Rowdy-themed cellphone holders, tea infusers, bottle toppers, bookmarks, golf tee holders, Christmas tree ornaments and a Rowdy piggy bank.
“The students’ products are often given away during department open houses and alumni events, and some – like bottle openers, cookie cutters, light switch covers and rulers/bookmarks – are being marketed in the university’s River Hawk Shop,” says Johnston.
“The course is intended to be offered to juniors, but as long as the prerequisite and corequisite subjects are met, any student is permitted to take it,” says Michael Shone, a graduate assistant in the Department of Plastics Engineering who has helped with the course for the past three years. “The current class has 50 students in it, and we’re looking forward to nine great projects this semester.”
“I’m really enjoying the course,” says Stephen Kender, a plastics engineering junior. “It really opens my eyes. For example, when I pick up a plastic water bottle, I know how it was designed and what different steps were involved in making it. I now have a better appreciation of how plastic products are put together.”
Fellow plastics engineering junior Jonathan Cabot agrees: “The course offers an exciting hands-on experience. Mold design and manufacturing is a valuable skill to learn, and will be very useful in my professional career.”
Students typically spend 2½ hours in lecture and nearly two hours in lab work each week. They get introduced to SolidWorks (computer-aided design and drafting software), Autodesk Moldflow Insight (finite-element analysis and simulation software) and Mastercam (computer-aided manufacturing software) to help them develop the necessary skills in designing and fabricating project components. They also learn how to use computer numerical controlled (CNC) milling machines as well as manual equipment like grinders, lathes, presses and ovens to produce their molds and the corresponding parts.
“The students gain valuable knowledge and hands-on experience in injection molding, mold making and analysis,” says Shone. “They become comfortable with the machines and terminology used in the industry, and it gives them the foundation to pursue mold engineering as a career or to work with mold engineers effectively. There is also an advanced mold design course, called PLAS.5760, which seniors and graduate students can take to further expand this foundation.”